Environmental Conservation
Environmental Management System
The DMC Group strongly believes that business activities and environmental conservation should be part of the same decisionmaking process. We implement our environmental management system into each business activity process to promote its environmental management.
Headed by the President and Vice President, the DMC Group ISO Promotion Committee was established as the highest organ of decision making for environmental management. The ISO Promotion Secretariat handles the management of factories, divisions, and business bases under the supervision of the ISO Promotion Committee. Each division establishes Quality and Environmental Plans and reports progress and results at monthly Quality and Environment Council meetings (and ISO meetings) that the President and Vice President attend to ensure the effective application of the PDCA cycle.(ISO会議)において、その達成結果ならびに進捗状況を報告することで、PDCAを回しています。
Internal Audit
The Group conducts annual audits by certified internal auditors to confirm conformance with ISO 14001 and the effective functioning of the environmental management system.
DMC holds meetings before and after audits to clarify priority items, confirm the content identified by auditors with the related divisions and departments while the ISO Promotion Secretariat shares issues to promote improvement throughout the DMC Group, and handles progress management of the issues until the next meeting aiming to improve the quality of internal audits and environmental activities performed by the DMC Group.
In-house Education
The DMC Group considers human resource development critical to the promotion of its environmental management activities. To this end we have established a curriculum, as shown below, to provide individual employee education based on specialization and level.
- ISO awareness training: All division managers provide opportunities for employees to recognize and learn quality and environmental policies in order to maximize business results by linking division goals and individual targets. Employees themselves record these details in the prescribed format where they are then managed by the ISO Promotion Secretariat (Group attendance rate: 100%).(グループにおける受講率100%)。
- Internal and external training related to CO² reduction: Training on greenhouse gas reduction case studies is conducted as part of CSR training, and training on procurement methods for raw materials and other items that contribute to the reduction of CO² emissions is conducted as part of CSR procurement training.
Material Balance
-
Electricity : 6,561thousand kWh
-
Renewable energy : 2,060thousand kWh
-
Fuel - Petroleum : 0thousand ℓ
-
Water withdrawal : 34thousand m³
- [ Major Materials ] Highly functional resin, plate glasses, etc.
-
Gasoline : 34kℓ
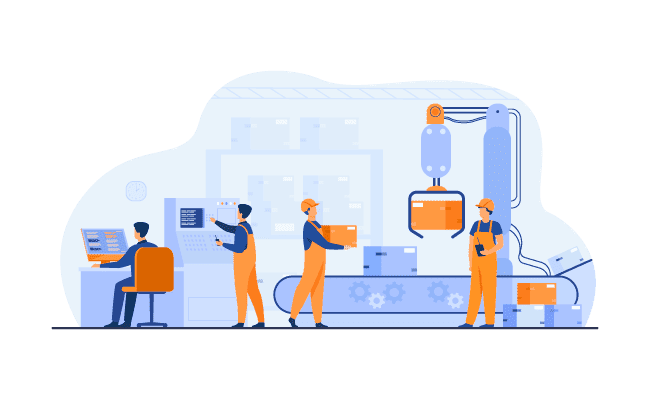

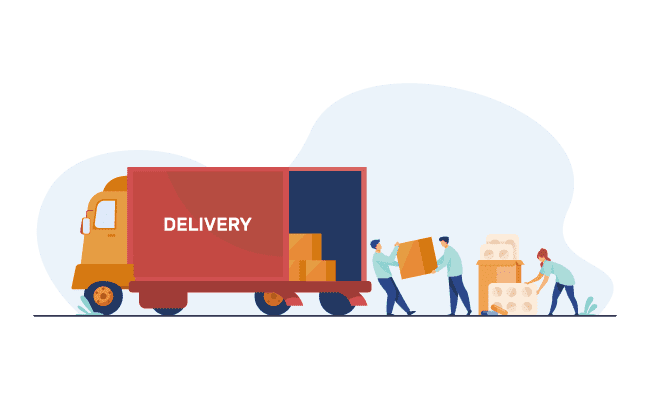
-
CO₂ : 3,268t-CO₂
-
Wastes : 198t
-
Water discharge : 33thousand m³
- [Products] Touchscreens, LCD modules
-
CO₂ : 88t-CO₂
Response to Climate Change
In the face of climate change, DMC considers the reduction of CO₂ emissions that contribute to increasing temperatures as our corporate responsibility and works toward this in all phases of the production and delivery of touchscreens through the effective use of energy and other approaches.
Progress Towards CO² Emissions Targets
Aiming to achieve carbon neutrality by 2050, the Group had set a target of a 26.6% reduction in CO² emissions by FY2025 (compared to FY2018 levels). Subsequently, reflecting the introduction of renewable energy-derived CO²-free electricity at the Shirakawa and Iwaki factories and a revision of our air conditioning operations as well as other factors, we changed our Scope 1 and 2 reduction target for FY2025 from 26.6% to 40.0% (compared to FY2018 levels). The reduction targets for FY2023 were 55% and 15% reductions compared to the base year for Scope 1 and 2 emissions, respectively. Our actual results for FY2023 were a 57% reduction for Scope 1 and a 36% reduction for Scope 2. The factors behind the Scope 2 emissions reduction included a change from wet etching to laser etching for some processes, a revision of air conditioning operations at our factories, and the introduction of CO²-free electricity derived from renewable energy sources. We will continue to strengthen energy conservation measures to promote CO² reductions.
Reduction of CO² Emissions throughout the Supply Chainn
The DMC Group calculates greenhouse gas emissions in all its corporate activities, from upstream to downstream, based on the GHG Protocol,an international standard for companies to calculate and report greenhouse gas emissions throughout their supply chains. In FY2023, Category 1 emissions, which account for the highest proportion of CO² emissions, decreased by 14% compared to the previous year. Although the merger led to an increase in the procurement of unit products, the reduction in bulk purchases due to changes in the external environment, and a decrease in the procurement of key raw materials for touchscreens due to lower production volumes are largely reflected. Clarifying emissions throughout our supply chain and identifying the potential for reducing emissions will lead to CO² reduction and contribute to the fight against global warming.
-
- * Scope is production sites (100% coverage). Including results from the Iwaki Factory from FY2021 and the Izumi Factory from FY2023
- * The figures for the base year have been revised in accordance with the incorporation of the Izumi Factory
- * CO²-free electricity derived from renewable energy has been excluded from Scope 2 emissions sources starting in 2023.
- * Scope is production sites (100% coverage). Including results from the Izumi Factory from FY2023.
-
FY2023 CO₂ Emissions by Scope & Category (t-CO₂)
Scope & Category Emissions SCOPE 1 88 SCOPE 2 3,268 SCOPE 1 + 2 3,356 SCOPE 3 19,090 Category 1 Purchased Goods and Services 12,834 Category 2 Capital Goods 293 Category 3 Fuel- and Energy-related Activities (not included in scope 1 or 2) 469 Category 4 Transportation and Delivery (Upstream) 1,029 Category 5 Waste Generated in Operations 6 Category 6 Business Travel 177 Category 7 Employee Commuting 430 Category 11 Use of Sold Products 3,852 Total 22,446 * Scope is production sites (100% coverage). Seedsware Corporation’s production site in Osaka is excluded from the scope as it was merged in 2023.
-
Management System & Operation
So that top management can directly involve themselves in the promotion of sustainability, we have established a Standards Management Office within the General Administration Department under the direct supervision of the President to develop companywide improvement activities. To date, we have shifted to LED lighting, switched to highly efficient PC monitors and other devices, and changed business vehicles to eco-friendly vehicles throughout the company. In addition, at the Iwaki Factory, we have achieved a 40% reduction in electricity use compared to the previous year by improving the use of air conditioning equipment (leading to an approximately 25% reduction in electricity use) and lowering operating hours.
Introduction of Electricity Derived from Renewable Energy SourcesWe are continuing to conduct energy-saving campaigns which call on our employees to conserve electricity. In addition, we are continuously working to improve the efficiency of energy use in production processes, and in FY2023, we introduced CO²- free electricity derived from renewable energy sources at the Shirakawa and Iwaki factories (ratio of electricity derived from renewable energy sources: 31.4%).
-
- * Scope is production sites (100% coverage). Including results from the Iwaki Factory from FY2021 and the Izumi Factory from FY2023
- * The figures for the base year have been revised in accordance with the incorporation of the Izumi Factory
Approaches to Waste Reduction
The DMC Group will make effective use of resources to create a sustainable, recycling-oriented society, and will set and work toward waste reduction and recycling targets.
-
Management System & Operation
DMC issues an industrial waste management manifest to monitor waste discharged from its factories and offices. We utilize an exclusive database to ensure uniform control over the management of disposal service providers and the industrial waste management manifest to continuously monitor the status of waste disposal. Because reducing the defect rate in production directly leads to waste reduction, efforts that DMC make for the improvement of production processes include the establishment of structures to maintain the best quality. We also striving to reduce the amount of waste by recovering and selling waste precious metals generated in the manufacturing process as valuable resources.
-
Approaches to Paper Reduction at DMC
The DMC Group digitalizes and shares documents, and manages decision-making processes, order sheets, and work hours by computer to reduce paper. Further, in 2023 we switched to electronic payments for our internal payment processing, and we are promoting the reduction of paper by through the use of electronic processing more than ever. We will continue working on reducing paper usage as part of efforts to improve our business processes and otherwise revise our business operations.
Water Resource Conservation
Infrastructure improvement has been delayed due to an increase in population and demand for water resources that have accompanied economic growth. This has accelerated water shortages and pollution, which has had a significant impact on our lives and environment. The DMC Group considers the effective use of water in manufacturing and the conservation of water resources.
Management System & Operation
-
The DMC Group established an integrated quality and environmental management system including the management of water to promote water resource conservation. We also apply the PDCA management cycle to improve environmental management. We are reducing the environmental impact of wastewater from production activities through the installation of facilities for proper treatment of wastewater from our factories and through the collection of wastewater by contractors. The Indonesia Factory has introduced and is operating a recycling system for water-intensive processes in order to make effective use of precious water resources, and is working to continuously reduce its water usage.
In addition, our domestic and Indonesian factories carry out appropriate wastewater treatment in accordance with laws and regulations, conduct regular biochemical oxygen demand (BOD) inspections, and submit test result certificates to public institutions to confirm that there are no problems.
Further, as part of our efforts to reduce our environmental impact, we are working to build sustainable manufacturing processes. In March 2024, we switched our etching process for all of our resistive touchscreen models to laser etching. Our intention with this change was to reduce our environmental impact and protect the environment by reducing the amount of water discharged in manufacturing. We expect to reduce wastewater volume at the Shirakawa Factory by approximately 55%, and at the Indonesia Factory by approximately 50%.
-
Reducing the Discharge of Chemical Substances
Management System & Operation
DMC works to reduce the use of chemical substances that may directly influence the environment through its production processes. No discharge or transfer of PRTR substances were detected in the fiscal year. We made the decision to change our etching process to laser etching in March 2024, and this is gradually being reflected in our products. This is expected to reduce our use of particularly deleterious solvents by approximately 70%.
Third-Party Assurance
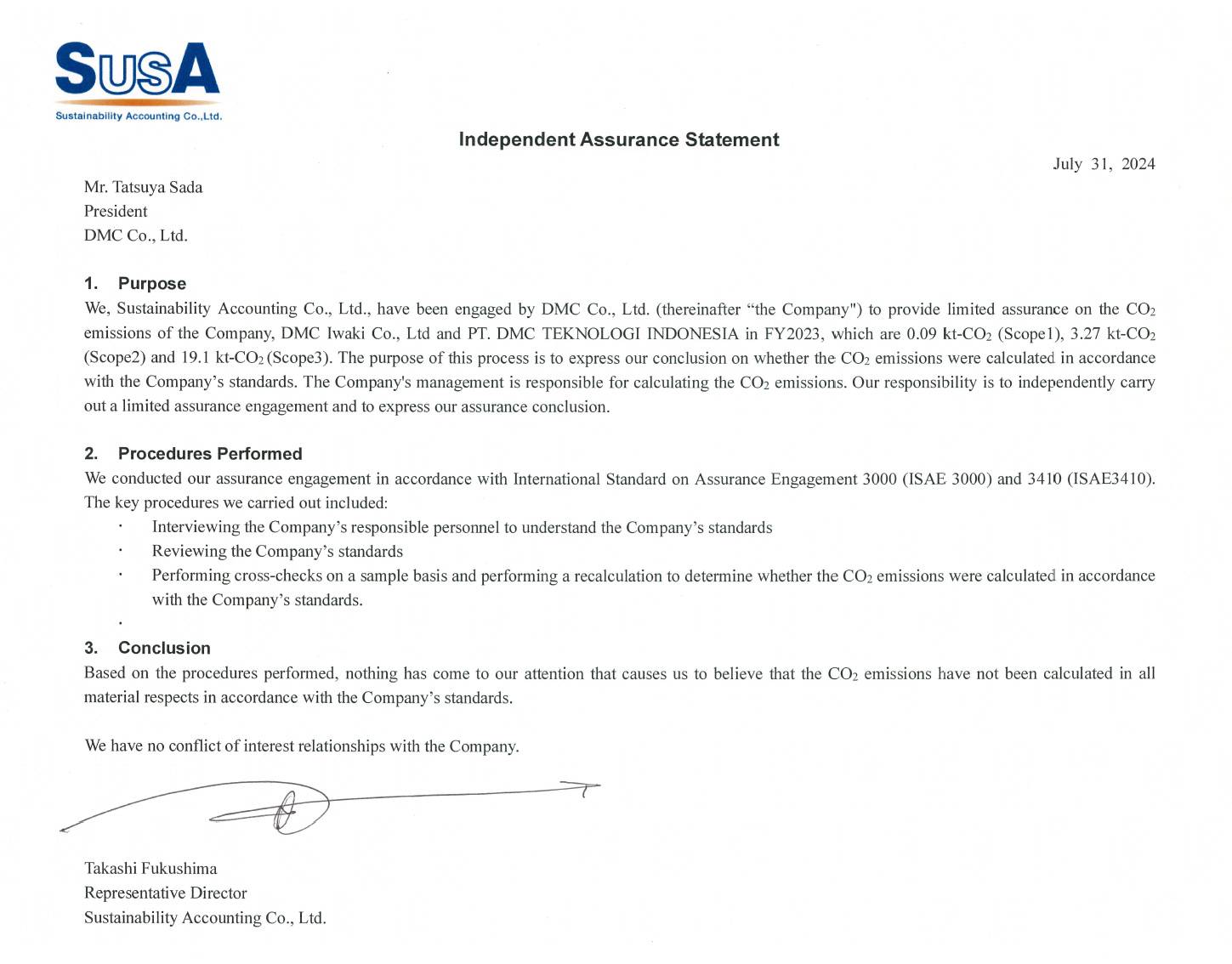